Wenn aus Pflanzen Treibstoff wird
Bioethanol wird wie andere Alkohole auch aus Pflanzen hergestellt. Die Prozessschritte unterscheiden sich jedoch abhängig vom Rohstoff: Ist er stärkehaltig, zuckerhaltig oder zellulosehaltig? Eine weitere Besonderheit ist die sehr hohe Reinheit des Ethanols, wenn er für Treibstoffe gedacht ist.
Alkohol ist nicht immer gleich Alkohol – und so sieht es auch mit der Herstellung desselben aus. Das Bioethanol, das als Treibstoffzusatz in Benzin gedacht ist, unterscheidet sich bereits bei den Rohstoffen von herkömmlichem Genussalkohol. Produziert wird Bioethanol aus dem Pflanzenzucker unter Zugabe von Hefepilzen und Enzymen. Das Produkt wird dann durch mehrstufige Destillation und Entwässerung auf mindestens 99,7 Prozent Alkoholgehalt gebracht. So die Kurzfassung. Je nach Rohstoffart müssen diese jedoch vor der Verarbeitung aufbereitet werden. Denn in Deutschland zum Beispiel wird Bioethanol hauptsächlich aus stärkehaltigem Getreide und zuckerhaltigen Zuckerrüben hergestellt. Eine dritte Möglichkeit sind zellulosehaltige Rohstoffe wie Stroh und Holzreste. Dieses Verfahren befindet sich jedoch noch in der Entwicklung.
Bevor der stärkehaltige Rohstoff (in diesem Beispiel Getreide) verarbeitet werden kann, wird er in einer Mühle zerkleinert. Warum? Weil aus der enthaltenen Stärke zunächst einmal Zucker werden muss. Das zerkleinerte Getreide wird im ersten Schritt mit Wasser und Verzuckerungsenzymen vermengt und erhitzt. Diese Mischung wird Maische genannt. Die hinzugefügten Enzyme spalten die Stärke auf und wandeln sie in Zucker um. Die Maische hat bereits einen Alkoholgehalt von etwa zwölf Prozent. Nun wird sie zusammen mit Hefepilzen im Fermenter der Bioethanolanlage vergoren.
Bei zuckerhaltigen Rohstoffen wie Zuckerrüben und Zuckerrohr (dieser wird vor allem in Südamerika verwendet) fällt dieser Schritt weg. Die Säfte werden direkt im Fermenter vergoren. Der Zucker wird zu Ethanol (C2H5OH) umgewandelt.
Den Alkohol vom Wasser trennen
Nun gilt es, den Alkohol vom Rest der Flüssigkeit zu trennen – das funktioniert über Destillation beziehungsweise Rektifikation. In einem thermischen Trennverfahren verdampft das Ethanol wesentlich früher als Wasser. Der verdampfte Alkohol wird aufgefangen und das Kondensat weiterverarbeitet. Dieser Schritt ist besonders wichtig bei der Verwendung als Treibstoffzusatz, weil Wasser im Tank langfristig dem Motor schadet. Daher reicht dieser eine Schritt nicht – denn die Rektifikation kann die Flüssigkeit nur bis zu einer Konzentration von 94,6 Prozent Ethanolgehalt reinigen. Der letzte Rest Wasser lässt sich nur noch mit Hilfe von Molekularsieben weiter konzentrieren – oder je nach energetischen Rahmenbedingungen auch durch andere Schritte wie Membranverfahren und Druckwechseladsorption. Dieser letzte Reinigungsschritt sorgt für eine Ethanolreinheit von mehr als 99 Prozent. So aufbereitet kann Bioethanol dann als fünf-, zehn- oder höherprozentige Beimischung zu Benzin verwendet werden.
Was aus dem ersten Prozessschritt übrig bleibt, ist die so genannte Schlempe, ein nährstoffreiches Koppelprodukt. Wird sie entwässert, getrocknet und pelletiert, eignet sie sich als hochwertiges Futtermittel. Alternativ kann die Schlempe auch im Fermenter einer Biogasanlage vergären und als Biogas in Strom und Wärme umgewandelt werden oder sie wird zu Biomethan aufbereitet und ins Erdgasnetz eingespeist.
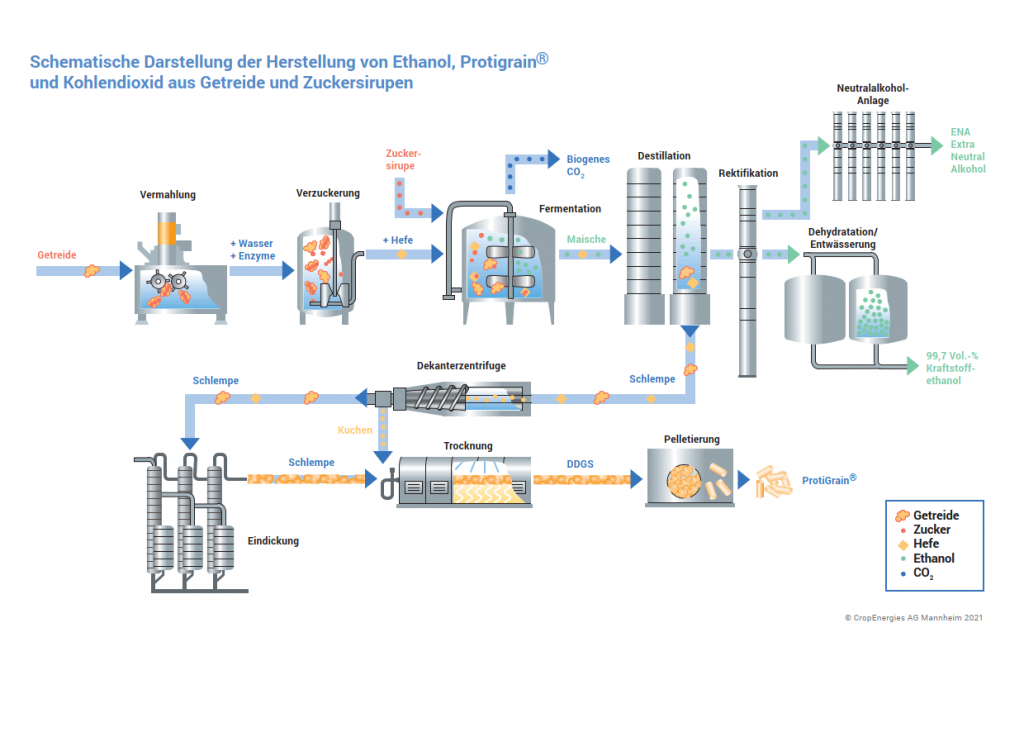